
It provides a different view of the balance sheet than other accounting methods such as first-in-first-out (FIFO). Calculate Ending Inventory Using the FIFO Method For most manufacturing operations, the costs that are included in an ending work in process inventory are raw materials or parts used, direct labor and manufacturing overhead. Often, this is the case when the manufacturing operation is short enough to allow all work in process to be completed when the period ends and current accounts are closed. However, this is very time-intensive, and generally, it is not done. It does not take into account added costs that may be incurred as work is completed, such as the cost of scrap, spoilage or the need to rework some items. This work in process formula yields an estimate, rather than an exact figure. An unusual fluctuation in the inventory turnover ratio or the average of inventory may signal problems with your purchasing policy or with your sales volume. The inventory turnover ratio and the average of inventory tell you how fast your inventory sells and the average amount of inventory you keep on hand.

The faster your inventory sells, the quicker you recoup your purchase costs and earn a profit. Calculating Ending Inventory – A Business Case: To calculate the ending inventory, the new purchases are added to the ending inventory, minus the cost of goods sold.
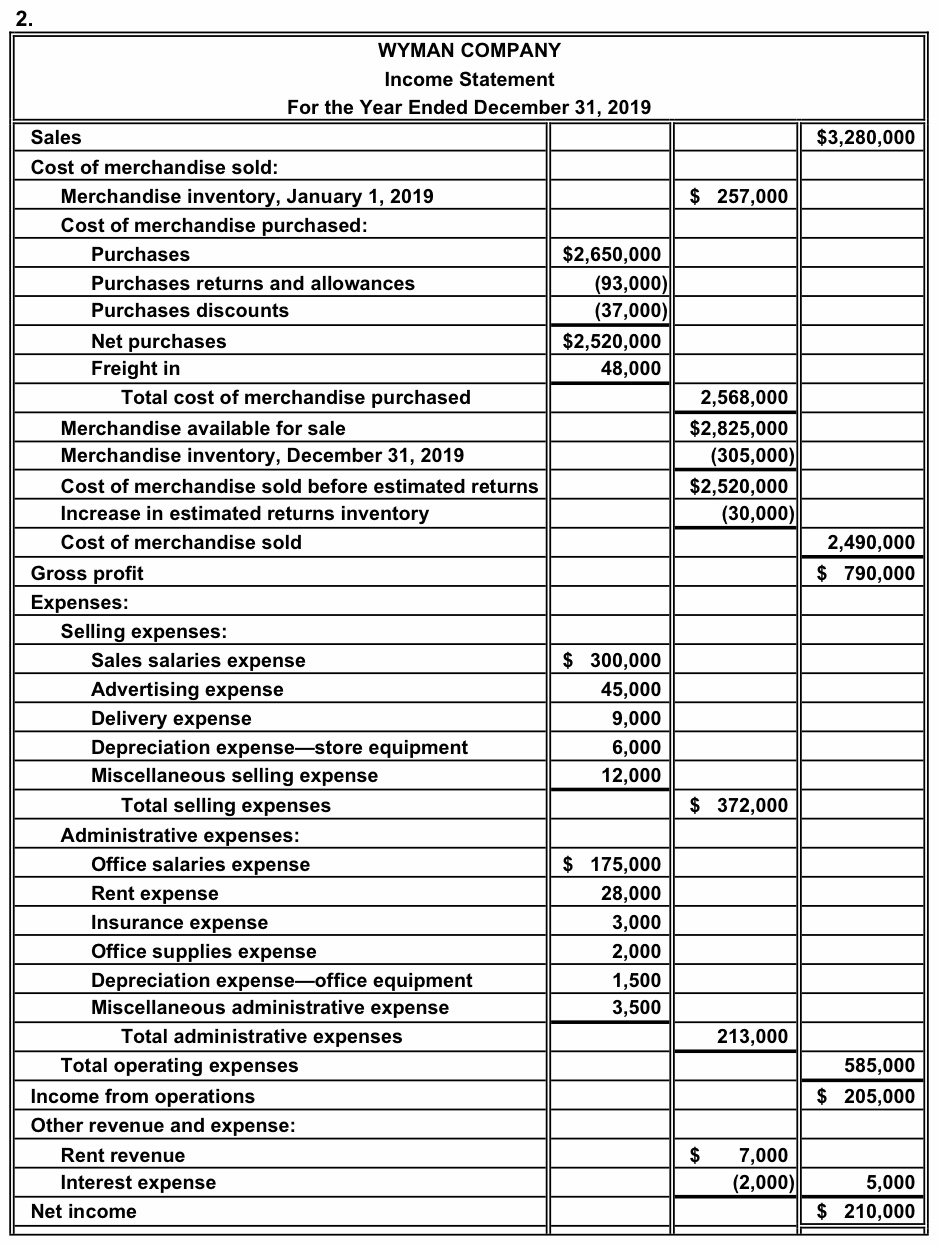
More commonly, the inventory change is calculated over only one month or a quarter, which is indicative of the more normal frequency with which financial statements are issued.
